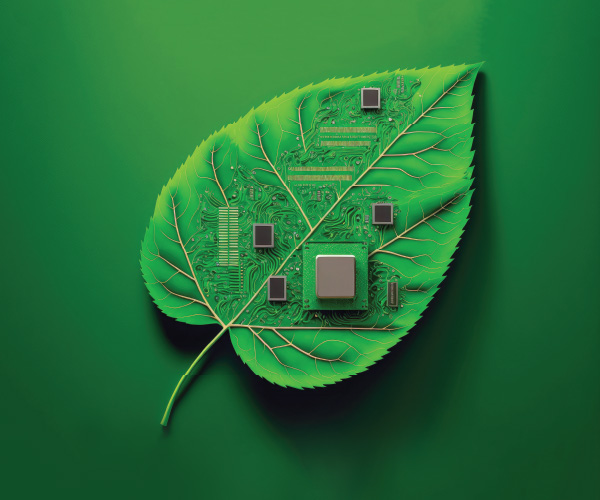
Tapping Tech to Bolster Sustainability
July 14, 2023
7 minute ReadAdvances in technology are enabling more productive and accountable sustainability practices.
By Lindsey Quick
Water preservation and other sustainability efforts have been a challenge — and a focus — for the car wash industry in years’ past. As technology continues to change every aspect of our lives and work, the same is true in implementing sustainability into car wash operations. Some car wash owners and equipment manufacturers are finessing this delicate balance, and using technology to further their sustainability and water-saving practices without compromising customer satisfaction. In fact, in some cases, it’s actually improving customer satisfaction.
Customize Every Drop With Sensors
While many organizations are introducing sustainability into their washes, some have implemented it across their entire process. One of those is Mister Car Wash, which has even partnered with Project Wet, a nonprofit organization, to help bring awareness to the benefits of conserving water within the car wash industry.
Jill Adams, vice president of marketing for Mister Car Wash, said the process starts the moment a vehicle enters the tunnel. “Sensors will detect the length of your vehicle, and from there, products are carefully timed and applied to match the specifics of your car with high-efficiency nozzles and specialized spray patterns that make use of every drop,” she said.
Like others, the water enters a reclamation process by working its way through settling tanks that remove heavy sediments, balance the pH and breakdown bacteria. The cleaned water from these tanks is then reused during the wash process, and any water that can’t be reused is safely returned to the city system. Mister also uses proprietary cleaning products that are free of phosphates and dyes.
As the vehicles exits the tunnel, they’ll pass through Mister’s Dynamic Dry system that uses air gates — equipment made possible with new, proprietary technology — to reduce energy consumption by reducing the number of times they turn on and off between vehicles in the tunnel.
Use RO Flow-On-Demand Technology
Another common sustainability practice is the implementation of reverse osmosis (RO) systems. Reverse osmosis is a process used to purify water using pressure to separate and remove unwanted contaminants and doesn’t use any environmentally hazardous chemicals as part of that process.
For Nathan Bertsch, managing partner at Express Carwash, the decision to implement a reverse osmosis system was made after hearing from their customers about their top concerns with car washes.
“When we polled our club members, we found that ‘spotting on mirrors’ and ‘spotting on rear-window glass’ were consistently two of the top five most common concerns that they wanted our car washes to address,” Bertsch said. “Installing an RO system was necessary for our customers because we found it was impossible to create a spotless finish without RO water.”
Express Carwash sees 185 to 220 cars per hour, and their 18 blowers and heated dryer room could only get vehicles so dry.
“Using RO water was the only thing that gave us confidence that those few droplets hanging on would dry to a spotless finish in the minutes after leaving our wash,” Bertsch said.
Bertsch had used RO units in the past that were built using components that were mostly intended for light commercial use. “They helped us to create a spotless finish, but they required preventative maintenance at 150,000- to 200,000-car intervals and were finicky,” he said. “Unexpected pump failures would leave us stuck without RO water available on a regular basis.”
So Bertsch went about looking for a more robust system and settled on the RO solution from Hoffman innovateIT.
“We had been looking for an effective reclaim system that was affordable, took up little backroom space, and would not cause tunnel odors and nozzle clogs,” Bertsch said. “The system from innovateIT met these expectations, and it is continually improving through real-time software updates.”
According to Hoffman CEO and ICA member Tom Hoffman, the system uses reverse osmosis “flow on demand” technology to create spot-free rinse water and reject water. “RO spot-free water usage is monitored and the system’s variable speed pump automatically adjusts to match production gallons per minute to the demand,” Hoffman said. “The more cars being washed, the more spot-free rinse water the system produces, allowing the pump to operate at lower pressures for longer periods when wash volume is low.”
With the new units, Express Carwash has been able to reduce freshwater usage from 45 to 32 gallons per vehicle. Bertsch said there are units on the market with higher flow rates, but he values the known performance consistency and elimination of odors and clogs. “We appreciate that we haven’t had days with downtime and haven’t needed to invest in expensive annual preventative maintenance,” he said.
Reclaim with a Twist
Spotless Wash Solutions President and CEO Jason Cunningham and his business partner, Josh Howa, were familiar with traditional water reclamation systems but wanted something that required less maintenance and repairs.
“Most conventional reclaim systems use a hydrocyclone separator to remove particles and debris from the reclaim water,” Cunningham said, where a pump is used to pull water from the reclaim pit. Cunningham and Howa wanted an alternative solution for their Big Splash Wash locations.
“We looked at different water treatment methods and opted to use a sump pump that is immerged in the reclaim tank itself to push water through the system,” Cunningham said.
The Spotless system also uses a nighttime trench flush pump with a proprietary self-cleaning filter system to continuously condition the reclaim water through a spine of mesh disc filters up to 140-micron mesh. “The spine assembly has a spring compression unit and an internal piston, which are used to alternately compress and release the discs during filtering and backflushing cycles,” Howa said.
The backflush feature allows the filter to self-clean throughout the day while feeding the wash a continuous supply of reclaim water, Cunningham said. He also noted that the disc filter limits the size of particles that are allowed to pass through the system.
“The control system isolates portions of the filter banks and self-cleans and purges the solid waste from the membranes for efficient operation and very low maintenance,” Howa said.
Next, a system of high-pressure and high-volume mud-blast pumps deliver the reclaim water to the tunnel arches and applicators. Between and during washes, the water is cycled through the system of conveyor trenches, trench drains and trash pits where the water is continuously oxygenated through aeration and returns to the reclaim tanks for additional settling and separation of solids. “This cycle is continuous during wash operating hours,” Howa said.
At Scrubs Express Wash, a more traditional reclaim system is used, but technology has enabled the filtration process to be tweaked to better control bacteria and odors, said ICA member Christine Kelly, operations manager. “The ERS-150 by Sobrite uses UV technology to destroy the bacteria and algae buildup that is the cause of most reclaim odor, in addition to reducing the amount of chemicals heading into our reclaim tank.”
Get Even Closer With High-Tech Dryers
While reimagining water usage and disposal might be the first idea that comes to mind when thinking about sustainability and a car wash, another option for sustainability efforts is that of energy consumption. Technology is making a difference in this space as well. Mark VII Equipment, a car wash equipment manufacturer, is focused on finding innovative ways of reducing energy usage for the blowers within a car wash.
“While each tunnel is different, generally speaking, roughly 50% of the electric consumption at a car wash is for the dryers,” said ICA member Pierre Leclercq, vice president of business development for Mark VII Equipment. Their Softline 2 product was developed by their German engineering team and was originally designed for European markets.
“Energy has always been much more expensive in Europe than in the United States,” he said. “After the second oil crisis in the late 1970s, the team developed the contour-following dryers as well as the linear technology to allow us to avoid hydraulic motors, which consume enormous amounts of energy and aren’t as easily controlled like electric motors.”
To make it work, Leclercq said the SoftLine 2 has dedicated photoeyes mounted to the dryer boom that pick up the signal of the vehicle presence and send it to the car wash system computer multiple times at high rates of speed. “The photoeyes allow the controller to create the shape of the vehicle,” said Leclercq. “In return, it allows the dryer boom to come very close to the car – reducing the need for more energy – without touching the car once.” He explained that the roof nozzle moves vertically to the car’s contours and can rotate up to 100 degrees, allowing it to align perfectly with the car.
“By getting closer to the car, we can use smaller motors,” he said. “For our 2+2 package, we use two horizontal contour-following dryers and two side dryers, which uses a total of approximately 27 kilowatts to dry a car. Compared to a 70-kilowatt standard dryer, that’s a 61% gain on electrical consumption for the dryers alone.”