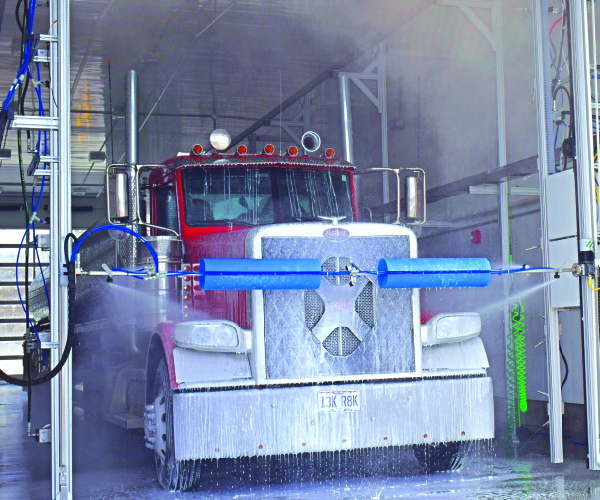
Smarter Equipment
October 29, 2022
11 minute ReadBy Nick Fortuna
Using Video Intelligence
When Tanuj Thapliyal, Rish Gupta and Sud Bhatija were graduate students at Stanford University, they recognized that cameras could do a lot more for businesses than just enhancing their physical security. So, in 2018, they founded Spot AI, a Burlingame, Caif.-based startup leveraging video intelligence to improve business operations.
Spot AI’s subscription service is used in a number of industries, including manufacturing, warehousing, healthcare and retail, but car wash operators might find it especially useful. That’s because the high-definition cameras and video-storage systems help car washes handle damage claims more efficiently, boost throughput in tunnels and improve employees’ performance.
Thapliyal, Spot AI’s chief executive, said the typical car wash might have 16 to 32 of his cameras installed throughout the tunnel, especially at the entrance and exit. The 5-megapixel cameras allow users to zoom in up to 16 times closer for a clear view of vehicles as they pass through the tunnel, enabling operators to determine whether vehicles actually sustained damage during the wash.
Car washes can store videos onsite for either 30 or 60 days using Spot AI’s artificial intelligence network video recorder, and if they want to save a video indefinitely, they just have to hit a button to store it on the cloud. Car washes have access to an unlimited number of saved videos for as long as they subscribe to Spot AI’s service, and they can download those video clips to local hard drives as a backup if they wish.
When a customer complains about damages, car wash operators can easily find video footage of that vehicle going through the tunnel. Using Spot AI’s case-management platform, operators can securely share that video with customers and their own insurance providers, along with comments and annotations.
Thapliyal said the platform helps car washes prove to customers that the scratches and dings on their vehicles, which may only be noticeable once the car has been cleaned, weren’t caused by the car wash. And in the rare case when an antenna gets bent or a rim gets scratched, the video can help car washes resolve those claims quickly.
By providing clear video footage promptly, car wash operators often can prevent customers from becoming so dissatisfied that they badmouth the business to their family, friends and neighbors, Thapliyal said.
“The operator can then go to the customer and say, ‘We’d love to give you a free coupon as a gesture of good faith, and we hope you give us another shot,’” he said. “So, you can transform a damage claim into a way to improve your brand within the community that you serve just by sharing the footage with the customer so that they can see that nothing actually got hit.”
Thapliyal said Spot AI’s system is easy to install, and car wash operators can either use their own security cameras or obtain free cameras from the company. At the end of the subscription term, car washes can even keep the cameras if they choose not to renew.
“If we’re not helping the customer, they shouldn’t be paying us for cameras at the end of the contract term, so it puts the onus on us to really serve them well,” Thapliyal said.
The cameras are resistant to dust and water and can withstand temperatures from minus 4 degrees to 140 degrees. The platform includes a feature that monitors the performance of cameras and detects when they’re nearing the end of their service life, at which pointSpot AI will ship new cameras to the car wash free of charge, Thapliyal said.
Users access the platform through a website or smartphone app. Free trials are available, and once they sign up, operators can pay monthly or annually, with costs typically averaging several thousand dollars a year, he added.
In addition to damage claims, the platform makes it easy for car wash operators to create teachable moments for employees. When a worker follows a best practice or fails to perform a task the right way, the operator can save that video and share it with workers at that location or companywide.
Using AI, the platform can monitor vehicles’ dwell time in the tunnel and measure throughput, so operators can compare the performance of multiple locations and identify operational issues. The system’s online dashboard allows operators to monitor live video feeds from multiple locations at once and to receive email notifications whenever an incident occurs.
Thapliyal said Spot AI updates its software frequently to include the latest features requested by clients. Later this year, the company hopes to unveil a new feature that will help car wash operators identify repeat customers who aren’t enrolled in an unlimited-wash program. When a license plate reader detects a repeat customer, the software will send an alert to workers, who can then reach out and encourage the customer to enroll in the wash club.
With new features coming roughly every two weeks, “the customer is getting an appreciating asset with us,” Thapliyal said.
Tyler Slaughter, chief operating officer at Camel Express Car Wash, with three locations in Tennessee, said he was “blown away” by a product demonstration and subsequently subscribed to Spot AI’s service.
“Spot AI helped me reduce the time to resolve damage claims from 72 hours to within 24 hours,” he said.
Cleaning Large Fleet Vehicles
Figuratively and literally, D&S Car Wash Equipment Co. made big news at the Car Wash Show, unveiling a new in-bay automatic wash system for trucks and other large fleet vehicles.
Installing the IQ Max requires a bay measuring at least 17 feet tall, 18 feet wide and 50 feet long. To determine how long a bay you’ll need, take the length of the longest vehicle that needs to be washed and add five feet.
The IQ Max can handle vehicles as large as tractor trailers, firetrucks and buses. Despite its name, the IQ Max–XL model is actually a bit shorter, requiring a bay that’s at least 14 feet tall. Like the IQ Max, it’s ideal for ambulances, midsized moving trucks, shuttle buses and work trucks such as plumbing, HVAC and tow trucks.
In many cases, drivers have to wait several hours to have their large trucks washed by hand, and all that idle time is costly to businesses. Conversely, the IQ Max can wash about four tractor trailers per hour, getting companies’ manpower and assets back on the road much more quickly, according to Jerry Canfield, chief innovation officer at D&S.
For operators with extra-large bays, fleet vehicles represent a major opportunity to earn repeat customers. There were 37.9 million trucks registered and used by U.S. businesses in 2019, including almost 4 million tractor trailers and straight trucks, according to the American Trucking Associations.
“With this system, we’re able to wash anything that’s street legal,” Canfield said.The IQ Max system is essentially a larger version of the IQ 2.0 touch-free system, which has been around for about 10 years, Canfield said. Its advanced components and proprietary software allow it to scan each vehicle, determining its size and shape, using three-dimensional mapping, “so it knows exactly what it’s washing,” he added.
Since the system knows the precise dimensions of the vehicle, it will make sure the top wand nozzles and rotating side wands always stay18 inches from the vehicle and are perpendicular to the surface they’re spraying. If the vehicle has a luggage rack, spoiler, trailer hitch, bug guard or items in the bed of a pickup truck, the IQ 2.0 system adjusts its wash profile accordingly.
Using algorithms, IQ 2.0 also can identify which section of the car it’s washing at any given time and tweak its washing action, Canfield said. For example, when the top wand is cleaning the grill and the front of the hood, which often collect dead insects, it will slow down and perform a sweeping motion back and forth, hitting insects directly from above and from “glancing angles to make sure we’re knocking all those bugs off,” Canfield said.
The IQ 2.0 soft-touch system has similar features. The 3-D mapping capability ensures that the same amount of brush material, about five inches, makes contact with the car’s surfaces throughout the wash, so the closed-cell foam brushes never apply too much pressure, Canfield said. The system also will adjust the spin direction and speed of brushes to avoid damaging side mirrors or ripping off wiper blades, antennas and bug guards, he added.
Using any smart device, car wash operators can access the IQ 2.0 system’s graphical user interface to program it remotely and review data such as daily wash counts and service issues. If a technical issue arises, the system automatically sends an alert to the operator’s smartphone or email account as well as the distributor, helping to maximize uptime.
The IQ systems cut down on water and chemical waste by applying those resources according to the exact dimensions of each vehicle, instead of using the same wash profile for each vehicle.
As a result, “there’s not a lot of overspray since all the nozzles are directed right at the car,” Canfield said. Vehicles get a customized wash in five to seven minutes.
“We’re basically never washing air,” he said. “We’re only ever washing the car, so we’re able to do it relatively quickly because we know exactly what the car looks like.”
Blasting Away Dirt
When Tom Hoffman Jr. isn’t helping to run Hoffman Car Wash, the family business his parents started in 1965, he’s got a fairly impressive side project. Hoffman is chief executive of innovateIT, a car wash equipment manufacturer based in Albany, N.Y., just like the family’s car wash chain, which now numbers about two dozen sites.
Among innovateIT’s high-tech products is the wheelblastIT system, designed for high-volume tunnel washes. Its three rotating zero-degree nozzles on each side of the car move horizontally on a metal frame, following the front wheel for five feet as the car travels through the tunnel, then moving back to its old position in time to start on the back wheel.
Unlike stationary arches that clean wheels as they pass by, wheelblastIT’s nozzles travel with the wheel for five feet, so the high-pressure spray hits wheels directly the whole time, instead of from side angles, Hoffman said. In addition, the wheelblast system automatically adjusts its speed to match that of the conveyor, so wheels are cleaned thoroughly and consistently.
The accuracy of the nozzles’ spray means that the typical car’s wheels are washed using only four gallons of water, Hoffman said.
“A lot of manufacturers have a way of blasting at wheels, but this has got the most contact time; it’s on the wheel longer and does a better job,” he said. “The stationary units use bigger nozzles in order to be as effective, so they tend to use more water than ours. We’re using small, high-pressure nozzles, and they’re rotating zero degrees, so it’s just a more effective wheel-cleaning system.”
A similar product from innovateIT, the blastIT high-pressure arch, is helping Hoffman Car Wash reduce its labor needs at a time when the minimum wage in New York state has climbed to $13.20 an hour and workers remain in short supply, Hoffman said.
The blastIT arch eliminates the need to have two or three workers using high-pressure guns to blast dirt off the sides of vehicles as they enter the tunnel, Hoffman said. The split manifold allows operators to use fresh water above the window line and reclaimed water below. Like the wheelblastIT system, the blastIT arch is electronically driven, so there are no hydraulic leaks, Hoffman said.
Since nozzles are attached to the arch, they don’t move horizontally with the car, like in the wheelblastIT system, but they do “oscillate back and forth” from left and right, spraying the car from different angles, Hoffman said. By streamlining the prepping process, the blastIT arch enables tunnel operators to wash more cars per hour, he said.
“Primarily, it’s a labor-saving piece of equipment, but it’s also helped us improve production,” Hoffman said. “Now, you don’t have an employee taking too much time over-prepping a car, wasting chemicals and water.”
Preventing Accidents In Tunnels
Boosting throughput is a top priority for operators, but loading cars too quickly can result in a game of bumper cars inside the tunnel —a common problem due to the growing number of vehicles with automatic emergency braking systems.
In response, Akron, Ohio-based DRB developed its NoPileups full-tunnel optimization system. Unlike other anti-collision systems that use loop pads or photo eye sensors to determine where a vehicle should be in the tunnel, NoPileups uses video and advanced computer technology to track where the vehicle actually is, according to DRB.
Some anti-collision products cover only the tunnel exit, but NoPileups protects cars throughout the tunnel and even 10 to 15 feet beyond the exit through its Smart Exit feature. NoPileups automatically stops the conveyor when an incident occurs and provides a 15-to 20-second video clip so operators can identify what caused an issue.
Smart Exit detects when a vehicle has stopped at the end of the conveyor, creating a collision threat, and automatically stops the conveyor. When the situation has cleared, the system automatically restarts the conveyor. Smart Exit is ideal for tunnels with a tight egress onto a busy road, belt conveyors, high-volume tunnels and full-service tunnels where cars are awaiting aftercare services, according to DRB.
DRB’s service team monitors the equipment and provides routine software updates and server maintenance. Operators get weekly reports allowing them to compare throughput at multiple locations, see how close vehicles are loaded during peak hours to ensure they’re maximizing throughput, identify the cause of stops so they can take action and address bottlenecks at the tunnel exit.
“Once you start measuring downtime, you will have more uptime,” said Carl Howard, president and chief operating officer at Autobell Car Wash. “That is a huge benefit, no question, and I think if you just took that one benefit and analyzed your accident data, you would see that stopping those accidents pays for this equipment right there. It doesn’t make sense that our equipment can’t stop before something bad happens.”
Howard said that for car washes with average customer volume, paying a worker to monitor what’s going on inside the tunnel at all times can be a considerable cost. “So, it’s great to have a system that can monitor any kind of danger or safety hazard that may occur,” he added. “Not only can you reduce the number of incidents that occur, you can also increase your efficiency and productivity by increasing your uptime.”