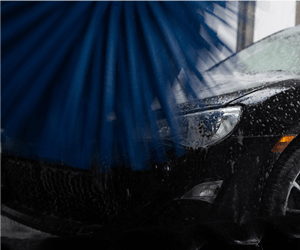
Creating the Car Wash Industry: An Inside Look
July 1, 2014
4 minute ReadBefore car culture exploded in the U.S., four-year-old Dan Pecora got his start in the family business, making brushes by hand with his father in the basement of their Milwaukee, Wisconsin, home.
By night Pecora’s father made brushes, and by day would sell them to anyone who would buy them. The year was 1948. Little did Pecora know that, over 60 years later, he would be the owner of one of the largest manufacturers of brush and vehicle detailing supplies to the international car wash industry, Chicago, Illinois-based Erie Brush.
The Pecora’s brush business grew along with 1950s car culture and the car wash industry, as America’s highways beckoned and hot-rodders rebuilt their cars and raced them into the future.
In the decades since, Pecora has seen plenty of change — in the car wash industry, in cars and car wash customers, in brushes — and has made his share of innovations along the way.
“I’ve seen the car wash industry adapt car conveyors from Henry Ford’s Detroit auto plants, when dozens of men labored by hand to clean inside and outside the vehicles,” Pecora said. “I’ve seen the rise of exterior only washes in the early 1960s develop into the automated, express washes with the entry gates of today. I’ve seen self-serve car wash bays proliferate.”
A BRUSH FOR EVERY SURFACE
One important change from the car wash customer’s point of view, according to Pecora, is a shift from a focus on white-wall tires to a focus on wheels.
“In the 1950s, drivers cared about keeping their tires’ 5-inch white walls spotless, which was tough to do when they rubbed up against a curb,” Pecora said. “Today, the focus is less on tires than on keeping custom wheels clean and shiny. That’s equally hard to do, when wheels can have so many hard-to-reach nooks and crannies.”
Having grown up with brushes in his DNA, so to speak, Pecora put his mind to creating two brushes for conveyor car washes specially designed to clean tires and wheels. With unique names like the “Wheel Wonder” and the “Poodle Brush,” these brushes’ filaments gradually vary in length between 4 to 7 inches to create a wave-like pattern, or resemble a well-manicured poodle. As a vehicle travels through the automated car wash, the longer bristles reach deep into wheel crevices while the shorter bristles clean the tire and wheel surface.
Pecora has provided car wash owners with brushes in a variety of materials over the decades: from natural fibers such as hog’s hair in the 1940s, to plastic extruded filaments such as polyethylene and nylon in the 1950s, to cloth materials in the 1960s and 1970s, to foam materials in the late 1990s.
To this day, Pecora provides car wash owners with automated and self-serve brushes made of all these materials and more.
“Keep in mind that brush materials from hog’s hair to polyethylene and nylon to cloth and foam all have their advantages in certain situations,” Pecora said.
Hog’s hair, it turns out — actual hog’s hair from a hog’s back, like the material Pecora made brushes from in his father’s basement as a child — is very soft and gentle, according to Pecora. Since the hairs are tapered, they are much softer at the tips for gentle washing. At the same time, the hog’s hair is durable and resilient despite bending and prolonged use. As such, one hog’s hair brush can outlive three or four less expensive options.
“Hog’s hair brushes dominate in self-serve car wash bays because they’re so soft to touch,” Pecora said. “Car wash customers appreciate this when they wash their own cars and are surprised by the softness, which won’t scratch the paint.”
“In conveyor washes, synthetic brush filaments like polyethylene work well when brush lengths up to 40 inches are required to accommodate a wide range of car widths for side washing,” Pecora added. “Cloth materials may be gentler on some cars. Since foam materials don’t absorb water, they are lighter, can operate on lighter equipment, and leave cars shiny.”
THE WASH EXPERIENCE
According to Pecora, as important as using the right tool for the job, whether machine, brush, or soap, is having intimate knowledge for what car wash customers want.
“Car wash owners know their customers want speed, convenience, quality and value,” Pecora said. “That means getting customers through quickly. But it can also mean a light touch, running rotating brush speed slower and soap/water solution higher. This can eliminate noise and roughness as the customer rides through the conveyor wash inside their own car, and that enhances the customers overall experience.”
“When over half of most conveyor wash customers are women today, not just men like when the industry started, creating a good experience for them is all the more important to keep them coming back,” Pecora said.
For more info, call 800-711-3743 (ERIE) in U.S., 773-477-9620 internationally; Fax 800-798-3743 (ERIE) in U.S., 773-477-6030 internationally; email sales@eriebrush.com; visit www.eriebrush.com; or write to Erie at 860 West Fletcher St., Chicago, IL 60657.