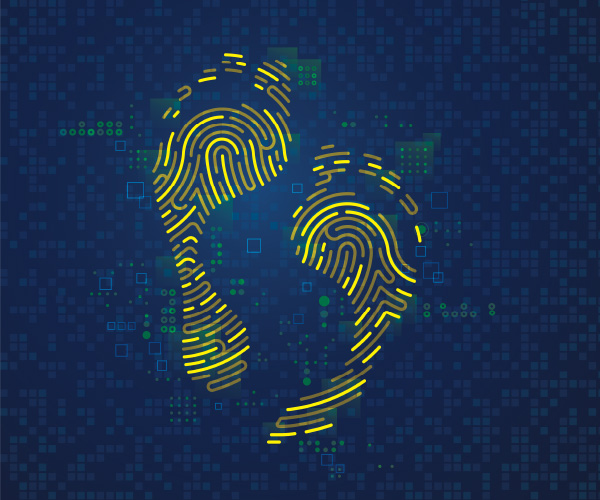
Safety Steps: One Tech at a Time
July 10, 2023
8 minute ReadTechnology is opening the door for innovative safety practices and products at car washes.
By Shaneen Calvo, Editor, CAR WASH Magazine
“We have a problem. It’s in the tunnel. Come quick!”
Words that will cause any car wash owner/operator’s blood pressure to rise, heart to skip a few beats and then tumble into your stomach.
Words that Jason Cunningham remembers hearing all too well at one of his car washes in the Kansas City area a few years ago.
With a sickening feeling as he imagined the worst, he rushed over to the tunnel to see the cause of the emergency call. It was like something out of a Car Wash 101 Nightmare Guide: one of the car’s tires was only partially on the belt when it loaded, causing the car to turn itself 180 degrees while in the middle of the tunnel. And, it was now facing the wrong direction in the tunnel.
Luckily, no one was hurt. The same could not be said of the equipment and the car, both of which suffered a lot of damage.
It only took this one incident for Cunningham, who owns Big Splash Car Wash in Colorado Springs, Colo. with his wife Claire, to get to work on figuring out a fix. But they couldn’t find an existing solution that met their needs. ”We tried lots of different things to get people to align their cars correctly — from road dots to lane delineators. But we had troubles with every option we tried,” Cunningham said.
“I knew belts had potential, but loading onto them was a problem, even though it’s supposed to be easier,” Cunningham said. “The alignment was an issue and there was no safety system available. We had our loaders, but they get distracted, sometimes. Or the customers are distracted and not watching them. Plus, everyone provides directions a little differently.”
So, the questions was: How could they create a system where technology controls how somebody gets on the conveyor?
Enter TESS, short for tunnel entry safety system, and Spotless Wash Solutions, the company the Cunninghams created to head up the research and development of the product, as well as the marketing and selling of it. The idea was to create a product that would allow for safe, unattended loading.
Following iteration after iteration, TESS is now guiding drivers at the entrance to Big Splash Car Wash.
On the exterior, TESS is two sleek electronics-filled towers that are placed on either side of the loading area. The big screen on each tower shows customers where their wheels are in relation to the belt. “The system is fully automated and gives customers direction to move left, right, pull forward, stop, car in neutral and so forth,” Cunningham said. The screen also provides a mirrored view so customers can see where their car tires are in relation to the belt.
And, one of the critical parts? “If they’re within about an inch or so of the conveyor edge, the conveyor will stop,” Cunningham said. “We can track the vehicle in relation to the wheel and tell where the wheel is on the belt. We can also detect roof racks, trailer hitches and other peripheral equipment on vehicles to help enable auto retracts, too.” They are also working on other enhancements to the system that will include dashboard reports on customer interactions and the “saves” that the system catches.
Following that scary call, TESS wasn’t the only safety feature the Cunninghams decided was a must-have at their car wash. The other was a technology-based safety measure called NoPileups™.
No bumping allowed
Bumping. So much fun when you’re pushing the pedal to the floor in a bumper-wrapped, 200-pound car in a padded, laser-light filled attraction. Not so much fun, and a serious safety issue, when bumping occurs between 4,000-pound cars inside your car wash tunnel.
This dilemma was the impetus for what has become a well-known product in the car wash industry: NoPileups. “They say the best ideas are born from solutions to real problems,” said Alex Mereness, DRB® director of NoPileups and tunnel strategic product management.
“He understood that reducing in-tunnel collisions could provide a safer car wash while increasing throughput and operational efficiency,” Mereness said about Pete Ness, who founded NoPileups in 2016.
NoPileups uses IP-based tunnel cameras and leverages computer vision, along with some machine learning, to visually track vehicles in the tunnel. If the system identifies a vehicle isn’t in its expected position, an emergency stop is triggered, shutting down the conveyor and other wash equipment and triggering a 15-20 second video so you can identify the cause of the issue. This concept was applied to tunnel exit safety concerns, as well, with the NoPileups Smart Exit solution, which works similarly but monitors 10-15 feet beyond traditional tunnel exit collision avoidance systems.
“The unique thing about the NoPileups solution is the continuous improvement configuration,” Mereness said. “Each time NoPileups stops a conveyor, our service team reviews the footage for the stop and determines if there are potential configuration changes that can be made to further optimize the system.”
In 2018, DRB acquired NoPileups. It is now installed in hundreds of car wash tunnels. “On average, the NoPileups system monitors over 15 million vehicles per month,” Mereness said. “Plus, sites that use NoPileups, on average, see a 95% reduction in collisions.”
Seeing is believing
Eeny, meeny, miny, moe … which one to choose? This video looks right, but there is something amiss in it. Maybe it is where she is standing? This one looks good, too, but are those cars being loaded too close together? There were four different videos to choose from, but only one showed the correct way of how to load cars to ensure maximum safety for the workers and the customers.
It is a safety training method being incorporated by some car washes using the Spot AI camera system, so employees can see multiple ways of handling the same thing.
“You can use video intelligence to help coach and train people. Help show them the best practices. You can record video of your best performing person and then share that with your newest hire. It helps people be the best versions of themselves,” said Tanuj Thapliyal, Spot AI’s CEO.
The program also allows notes and annotations to be written on top of these videos and tags to be incorporated. “You can pinpoint exact causes of an incident and tag the right team members in the video,” said Rish Gupta, co-founder and VP of product at Spot AI.
This feature came about because of how Spot AI views safety. “The way we think about safety is about how we can be proactive about preventing incidents in the first place,” Gupta said. “This enables car washes to use incidents that have happened in the past to prevent future incidents.”
The cameras are also used to keep track of the number of people in the tunnel and the number of times someone goes into the tunnel. “That allows car wash operators to make sure people are not in places where there is a higher incident of safety issues happening,” Gupta said.
While there are multiple camera systems on the market now, Gupta said Spot AI’s underlying technology is different because it uses a lot of powerful graphics processing units (GPUs), which accelerates the rendering of 3D graphics, and it uses more video artificial intelligence. This equates to more agility and higher velocity, Gupta said.
In 2023, interoperability will be the big push. “We are working on exposing a bunch of application programming interfaces (APIs) to work with other tools and systems,” Gupta said. APIs enable software components to communicate with each other, so you use them to help all of your systems work logically — and safely — together.
Gupta envisions camera systems, and this type of technology, becoming an invaluable part of car wash safety culture. “You are kind of having safety in a box,” he said. “Instead of having a safety officer at a car wash, we’ll have cameras that can identify and prevent common safety mishaps.”
Chemicals: Necessary but not necessarily dangerous
When it comes to the chemistry in play at the wash, technology is helping reduce the need for some of the more aggressive products that require special handling.
“You’ve seen how dirty car wash bays can look,” said ICA member Kipp Kofsky, president of Arcadian. “The cleaning and maintenance process involved in cleaning car wash bays usually requires the use of acid-based products to get the job done. This means using hydrofluoric, hydrochloric, sulfuric, phosphoric and muriatic acids. Hydrofluoric acid is one of the most dangerous acids you can come into contact with. If you are anywhere near that, you should be wearing a hazmat suit.”
So, no surprise that this necessary job doesn’t always have willing participants. “Employees didn’t really want to do it, and they would avoid doing it,” Kofsky said.
But technology is enabling the mixing, dosing and use of chemicals at car washes to be safer. “Through the use of newer technologies that weren’t previously available, we’ve been able to formulate these proprietary products that are safer compounds than the traditional harsh acids,” Kofsky said. “While we don’t recommend you stick your hand in it, these compounds have reduced car washes’ workers’ comp claims and lost time injuries, in addition to improving attendance.”
Innovation and technology have also come into play with the chemical storage and disbursement systems. One option uses a closed loop, sealed system that seals the top of the drum in which the chemicals are stored, creating a vacuum so no chemicals can splash out. A foot valve is used to suck the chemical out of the container. This type of system won’t allow the chemical to be released until the car wash system needs the chemical to be drawn out of the container, Kofsky said. “So, if the container gets accidentally pushed or tilted, the chemical won’t come out the top of the drum.”
But safely working around any type of chemical requires more than safer processes, systems and compounds. It requires crews to wear proper PPE and be cognizant of the dangers. “If you are in the room where the chemicals are being stored, wear chemical resistant gloves and suit,” Kofsky said. Also, make sure there is a safety data sheet on the premises. “The safety data sheet outlines how to treat chemical exposure, which is vital to have accessible and handy should exposure occur,” Kofsky said. “They need to have it accessible to all their employees. It’s the law.”